Introduction:
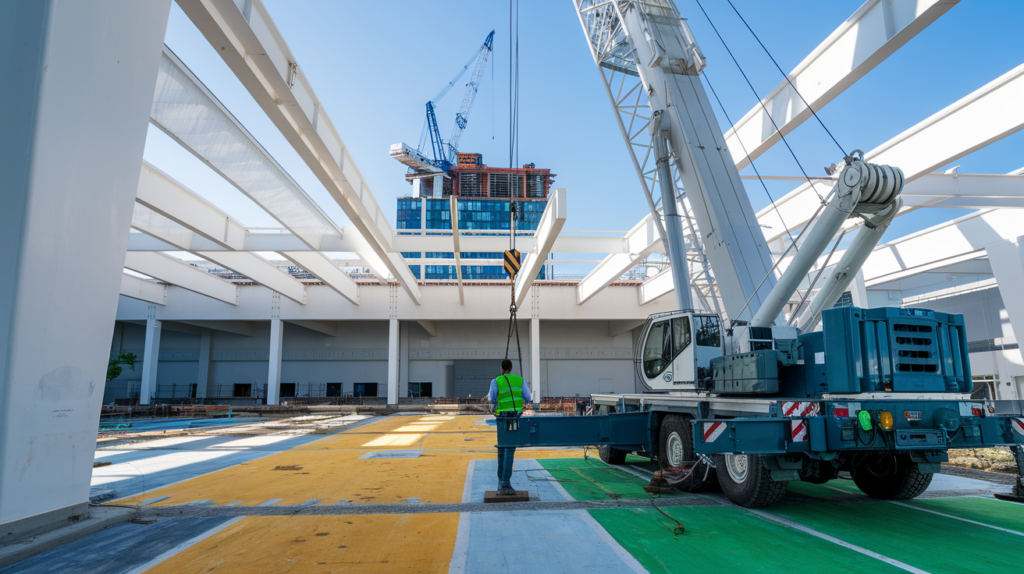
Cranes are indispensable on construction sites, performing heavy lifting and moving tasks that are essential for building modern infrastructure. However, they also pose significant risks, with crane-related accidents often resulting in serious injuries or even fatalities. Ensuring crane safety is not just about adhering to regulatory standards but also about implementing a comprehensive safety culture on construction sites. This blog will cover the best practices that construction companies should adopt to maximize crane safety, minimize accidents, and ensure the well-being of all workers on-site.
The Importance of Crane Safety
Construction sites are high-risk environments, and cranes contribute to some of the most dangerous operations due to the heights, heavy loads, and complex maneuvers involved. Crane-related accidents can occur due to various factors, such as equipment failure, improper setup, weather conditions, or human error. By following strict safety protocols and ensuring that all workers are properly trained, companies can significantly reduce the likelihood of accidents.
In addition to protecting human lives, prioritizing crane safety helps companies avoid costly downtime, legal liabilities, and damage to reputation. Safety should always be the top priority on construction sites, and crane operations require special attention given their inherent hazards.
Common Crane Hazards on Construction Sites
Understanding the common hazards associated with crane operations is the first step in preventing accidents. Below are some of the most frequent dangers:
1. Overloading
One of the most common causes of crane accidents is overloading, where the crane is tasked with lifting more weight than it is designed to handle. This can lead to structural failures or tipping over, endangering both the operator and workers nearby.
- Solution: Always ensure the crane’s load is within its capacity. This requires proper load monitoring systems and adherence to the crane’s load chart specifications.
2. Improper Assembly or Setup
Setting up a crane incorrectly can lead to catastrophic accidents. Cranes that are not leveled or anchored properly are at risk of tipping over or collapsing during operation.
- Solution: Ensure cranes are set up according to manufacturer specifications, on firm and level ground, with proper outriggers in place. Site inspections and regular checks are essential to verify that cranes are properly assembled.
3. Falling Loads
If a crane’s load is not properly secured, it can slip and fall, potentially injuring workers or damaging property below.
- Solution: Use appropriate rigging techniques and equipment to secure loads. Workers responsible for rigging must be properly trained, and the rigging equipment should be inspected before each lift.
4. Weather Conditions
Strong winds, lightning, and other severe weather conditions can create dangerous situations for crane operations. Wind is especially problematic, as it can cause cranes to sway or even topple if not properly managed.
- Solution: Monitor weather conditions closely, and avoid using cranes in high winds or during storms. Establish protocols for halting operations when conditions become unsafe.
5. Electrical Hazards
Cranes often operate near power lines, creating a risk of electrocution if the crane or its load comes into contact with the lines.
- Solution: Maintain a safe distance from power lines at all times. Use spotters and warning systems to ensure that crane booms and loads remain clear of overhead electrical lines.
Best Practices for Crane Safety
1. Comprehensive Training for Operators and Workers
Ensuring that all crane operators and workers involved in crane operations are properly trained is critical to preventing accidents. Training should cover not only crane operation but also safety protocols, hazard recognition, and emergency procedures.
- Operator Certification: Crane operators should hold proper certifications, as required by local regulations and industry standards. This ensures they are qualified to operate specific types of cranes.
- Ongoing Training: Even experienced operators should undergo regular refresher training to stay updated on the latest safety standards, equipment advancements, and techniques.
- Worker Education: All workers on the construction site should be educated about crane safety, including how to avoid working under suspended loads and how to recognize potential hazards.
2. Regular Inspections and Maintenance
Regular inspections and maintenance are essential to keeping cranes in safe working condition. This includes daily inspections by the crane operator, as well as periodic, more thorough inspections by qualified technicians.
- Daily Inspections: Operators should perform daily checks before using the crane. These checks should cover key components like the boom, hoist, load hooks, cables, and brakes. Any signs of wear or damage should be addressed immediately.
- Scheduled Maintenance: Cranes should undergo regular maintenance according to the manufacturer’s guidelines. This includes lubrication, part replacements, and system calibrations to ensure the crane is functioning correctly.
3. Proper Load Handling and Rigging
Improper load handling and rigging are leading causes of crane accidents. It is essential that all loads are securely attached, balanced, and within the crane’s lifting capacity.
- Certified Riggers: Only certified riggers should be responsible for attaching loads to the crane. They should be trained in load dynamics, slinging techniques, and the proper use of rigging equipment.
- Balanced Loads: Loads should be evenly distributed to avoid imbalance. Swinging or unbalanced loads can destabilize the crane or cause the load to fall.
4. Safe Operating Procedures
Crane operators must follow safe operating procedures at all times, including proper signaling, load handling, and communication with other workers on-site.
- Use of Spotters and Signalers: A dedicated spotter or signaler should assist the operator by providing clear, standardized signals during crane operations. This is especially important when the operator’s view is obstructed.
- Load Path Clearance: The operator must ensure that the load path is clear of workers, equipment, and other potential obstructions. No one should be allowed to walk under a suspended load.
5. Creating a Safety Culture
Safety should be a core value on any construction site, with a focus on proactive measures rather than reactive ones. This involves cultivating a strong safety culture where all workers are encouraged to prioritize safety and report any potential hazards.
- Safety Meetings: Regular safety meetings or “toolbox talks” should be held to discuss crane safety and other site-specific hazards. These meetings help reinforce the importance of safety and allow workers to raise any concerns.
- Hazard Reporting Systems: Establish a system for workers to report safety hazards or equipment issues anonymously if needed. Promptly address all reported concerns to maintain a safe working environment.
Crane Safety Regulations and Standards
Crane safety is governed by a number of national and international regulations that construction companies must comply with. These regulations are designed to ensure that cranes are operated safely and that all workers involved in crane operations are protected.
- OSHA Standards: In the United States, the Occupational Safety and Health Administration (OSHA) has strict guidelines regarding crane safety. These include requirements for operator certification, crane inspection, and load handling.
- ISO Standards: The International Organization for Standardization (ISO) also provides guidelines for safe crane operation. ISO standards focus on crane design, inspection, maintenance, and safety during lifting operations.
- Local Regulations: Different countries and regions may have their own crane safety regulations. It is essential for construction companies to understand and adhere to all applicable rules and standards.
Leveraging Technology for Crane Safety
1. Load Monitoring Systems
Advanced load monitoring systems can help ensure that the crane is not overloaded. These systems provide real-time data on the weight of the load being lifted, preventing the crane from exceeding its capacity.
- Load Moment Indicators (LMIs): LMIs provide real-time feedback to operators about the load’s weight, the boom’s angle, and other factors that influence lifting capacity.
2. Collision Avoidance Systems
Collision avoidance technology uses sensors and cameras to detect obstacles in the crane’s path, helping to prevent accidents.
- Proximity Sensors: These sensors alert the operator when the crane is approaching a dangerous object or obstacle, enabling them to take corrective action before a collision occurs.
3. Remote Control and Automation
Crane automation and remote control systems can enhance safety by allowing operators to control cranes from a distance, away from potential hazards. Automation can also reduce the risk of human error by allowing the crane to perform certain tasks autonomously.
Conclusion:
Crane safety is a critical aspect of construction site management that should never be overlooked. By adhering to best practices such as proper training, regular inspections, safe operating procedures, and the use of advanced technologies, construction companies can significantly reduce the risk of crane-related accidents. Ensuring crane safety not only protects workers but also contributes to the overall success and efficiency of construction projects. A strong commitment to safety is essential for maintaining a productive and safe working environment on any construction site.