Introduction:
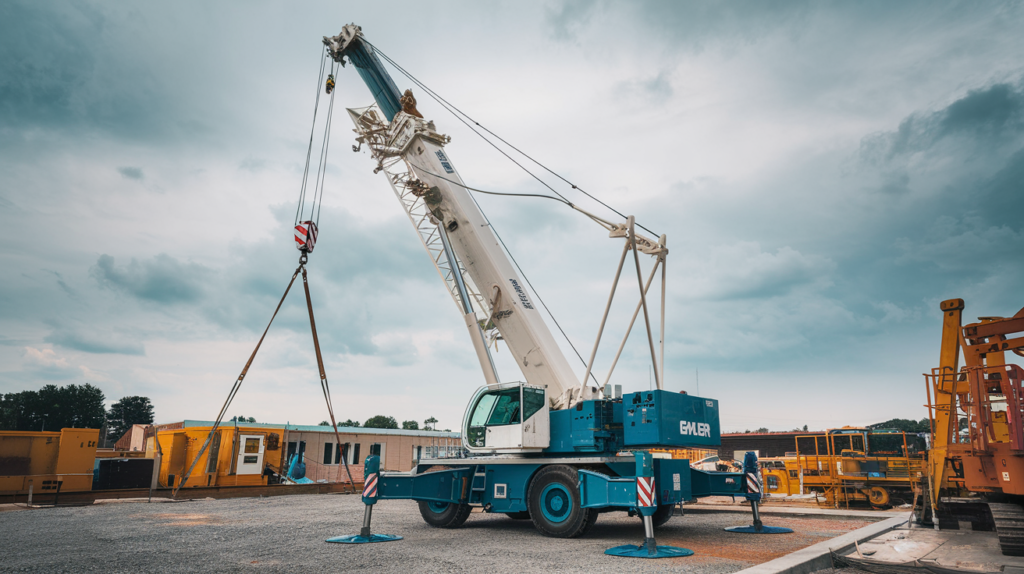
Proper crane maintenance is essential for ensuring the safety, efficiency, and longevity of these critical pieces of construction equipment. Regular maintenance not only helps prevent equipment failures and accidents but also extends the crane’s operational life and reduces long-term costs. This blog will explore the key aspects of crane maintenance, including routine inspections, preventive measures, and the importance of keeping cranes in top condition for safe and effective operation.
Importance of Crane Maintenance
1. Safety
Safety is the primary reason for regular crane maintenance. A well-maintained crane is less likely to experience mechanical failures, which can lead to dangerous accidents on construction sites.
- Accident Prevention: Regular maintenance helps identify and address potential issues before they lead to equipment failures or accidents.
- Compliance: Adhering to maintenance schedules and safety regulations ensures that the crane meets industry standards and legal requirements.
2. Operational Efficiency
A crane that is regularly maintained operates more efficiently, leading to smoother and more productive construction processes.
- Reduced Downtime: Proper maintenance reduces the likelihood of unexpected breakdowns, minimizing downtime and keeping the project on schedule.
- Enhanced Performance: Well-maintained cranes perform better, with fewer disruptions and more reliable lifting operations.
3. Cost Savings
Investing in regular maintenance can save money in the long run by preventing costly repairs and extending the crane’s lifespan.
- Lower Repair Costs: Addressing minor issues through regular maintenance can prevent them from escalating into major, costly repairs.
- Extended Equipment Life: Routine upkeep helps ensure that the crane remains in good working condition for a longer period, maximizing the return on investment.
Key Aspects of Crane Maintenance
1. Daily Inspections
Daily inspections are crucial for identifying any immediate issues with the crane before it is put into operation. These checks should be performed by the crane operator or a designated inspection team.
- Visual Checks: Inspect the crane for visible signs of wear or damage, such as leaks, cracks, or loose components.
- Functional Tests: Test the crane’s controls, brakes, and safety systems to ensure they are functioning correctly.
2. Routine Maintenance
Routine maintenance involves regular servicing and inspections according to the manufacturer’s recommendations and industry standards.
- Scheduled Service: Follow the manufacturer’s maintenance schedule for tasks such as lubricating moving parts, replacing filters, and checking fluid levels.
- Component Inspections: Regularly inspect critical components such as the boom, hoist, cables, and load hooks for signs of wear or damage.
3. Preventive Maintenance
Preventive maintenance aims to address potential issues before they cause equipment failures. This proactive approach helps maintain the crane’s performance and safety.
- Predictive Analysis: Use predictive maintenance techniques, such as vibration analysis or thermal imaging, to identify potential issues before they become critical.
- Part Replacements: Replace parts that are nearing the end of their useful life, such as worn-out cables or hydraulic seals, to prevent failures.
4. Corrective Maintenance
Corrective maintenance involves repairing or replacing components that have already failed or are not functioning correctly.
- Immediate Repairs: Address any issues identified during inspections or operation as soon as possible to prevent further damage or safety risks.
- Component Overhaul: Perform major repairs or overhauls on components that have experienced significant wear or damage.
Maintenance Procedures and Best Practices
1. Follow Manufacturer Guidelines
Always adhere to the maintenance procedures and intervals specified by the crane’s manufacturer. This ensures that maintenance tasks are performed correctly and that the crane remains in optimal condition.
- Service Manuals: Refer to the crane’s service manual for detailed instructions on maintenance tasks and schedules.
- Authorized Service: Use authorized service providers or technicians for major repairs or inspections to ensure compliance with manufacturer standards.
2. Keep Detailed Records
Maintaining detailed records of all maintenance activities helps track the crane’s condition and history, making it easier to identify patterns or recurring issues.
- Maintenance Logs: Record all inspections, repairs, and service activities in a maintenance log or software system.
- Historical Data: Review historical maintenance data to identify trends or recurring problems that may require further investigation.
3. Train Personnel
Ensure that all personnel involved in crane maintenance are properly trained and qualified to perform their tasks.
- Certification: Technicians should hold relevant certifications and training to work on cranes and related equipment.
- Ongoing Training: Provide ongoing training to keep maintenance staff updated on new techniques, technologies, and safety practices.
4. Implement Safety Protocols
Follow safety protocols during maintenance activities to protect personnel and ensure that the crane is safe to operate.
- Lockout/Tagout Procedures: Implement lockout/tagout procedures to ensure that the crane is properly shut down and secured during maintenance.
- Safety Gear: Use appropriate safety gear, such as helmets, gloves, and eye protection, during maintenance tasks.
Common Maintenance Challenges and Solutions
1. Wear and Tear on Components
Over time, components such as cables, gears, and bearings can experience wear and tear, leading to decreased performance and potential failures.
- Solution: Regularly inspect and replace worn components before they fail. Use high-quality replacement parts and follow manufacturer recommendations for maintenance.
2. Hydraulic System Issues
Hydraulic systems are critical for crane operation but can be prone to leaks, pressure drops, and other issues.
- Solution: Check hydraulic fluid levels and inspect hoses and fittings for leaks. Address any issues promptly to maintain system performance.
3. Electrical Problems
Electrical issues, such as faulty wiring or malfunctioning controls, can affect crane operation and safety.
- Solution: Regularly inspect electrical systems and connections. Use trained technicians to diagnose and repair electrical problems.
Conclusion
Crane maintenance is a vital aspect of ensuring the safety, efficiency, and longevity of construction equipment. By following regular maintenance procedures, addressing issues proactively, and adhering to manufacturer guidelines, construction companies can keep their cranes in top condition and avoid costly repairs or accidents. Investing in proper maintenance not only enhances safety and performance but also maximizes the crane’s operational life and contributes to the overall success of construction projects. Prioritizing crane maintenance is an essential step in maintaining a safe and productive construction site.